GHS conversion affects every individual and company that deals at all with chemicals in the course of their business, but the specifics of who must go through the process of MSDS to SDS conversion can be fairly confusing.
When we talk about “GHS Conversion,” we are discussing the transition from current material safety data sheets to new GHS-formatted safety data sheets. By June 2015, everyone who handles chemicals must have new SDSs for every substance they use, even those that are not frequently in use.
Just because you must have SDSs on site does not mean you are required to create them in-house. Many distributors have been confused by the terminology of the new standards, believing that they must spend the time and effort to perform the GHS conversions (even if they did not originally create the materials themselves) to ensure the final documents include their own company branding and contact information.
The real burden of GHS SDS creation falls on the manufacturers. Those companies that create or blend a chemical bear responsibility for its documentation. If you do not create a chemical, you do NOT have to create its SDS. The manufacturers should supply all the chemical’s downstream users with the proper safety data sheets, ideally as early as possible. Those receiving the SDSs are still responsible for implementing them into their systems and making sure all labels are also GHS compliant.
Companies should be proactive, no matter what size or what degree of separation from the manufacturing of the chemicals they are, and should seek to be GHS compliant as soon as possible, rather than waiting until the last moment to make sure that their SDSs, labels, and practices are all up to date according to UN GHS specifications.
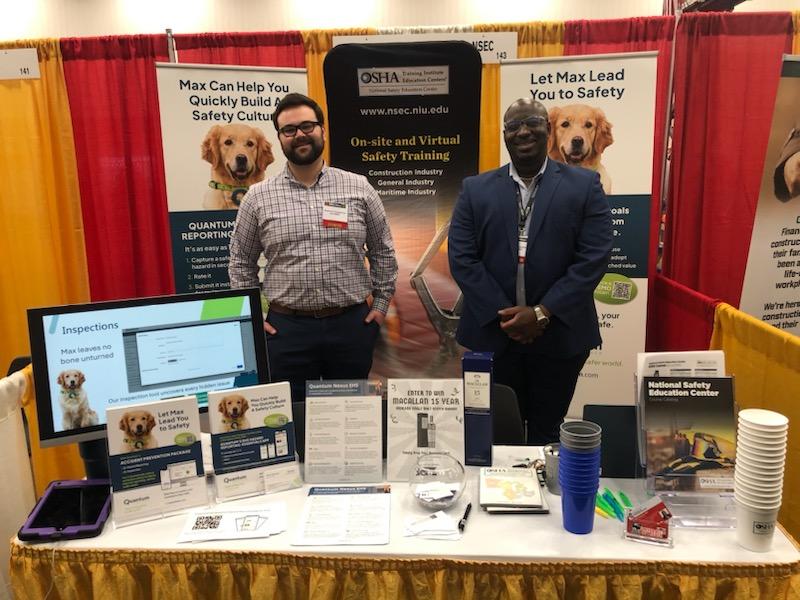