July Issue no. 1 – Prepare Your Business for Compliance
Understanding the ever changing nature of regulatory compliance is critical for employers to provide safe working conditions as well as avoid costly fines. We’ve compiled some blogs to help you gain insight on how recent changes can affect you, your employees, and your business.
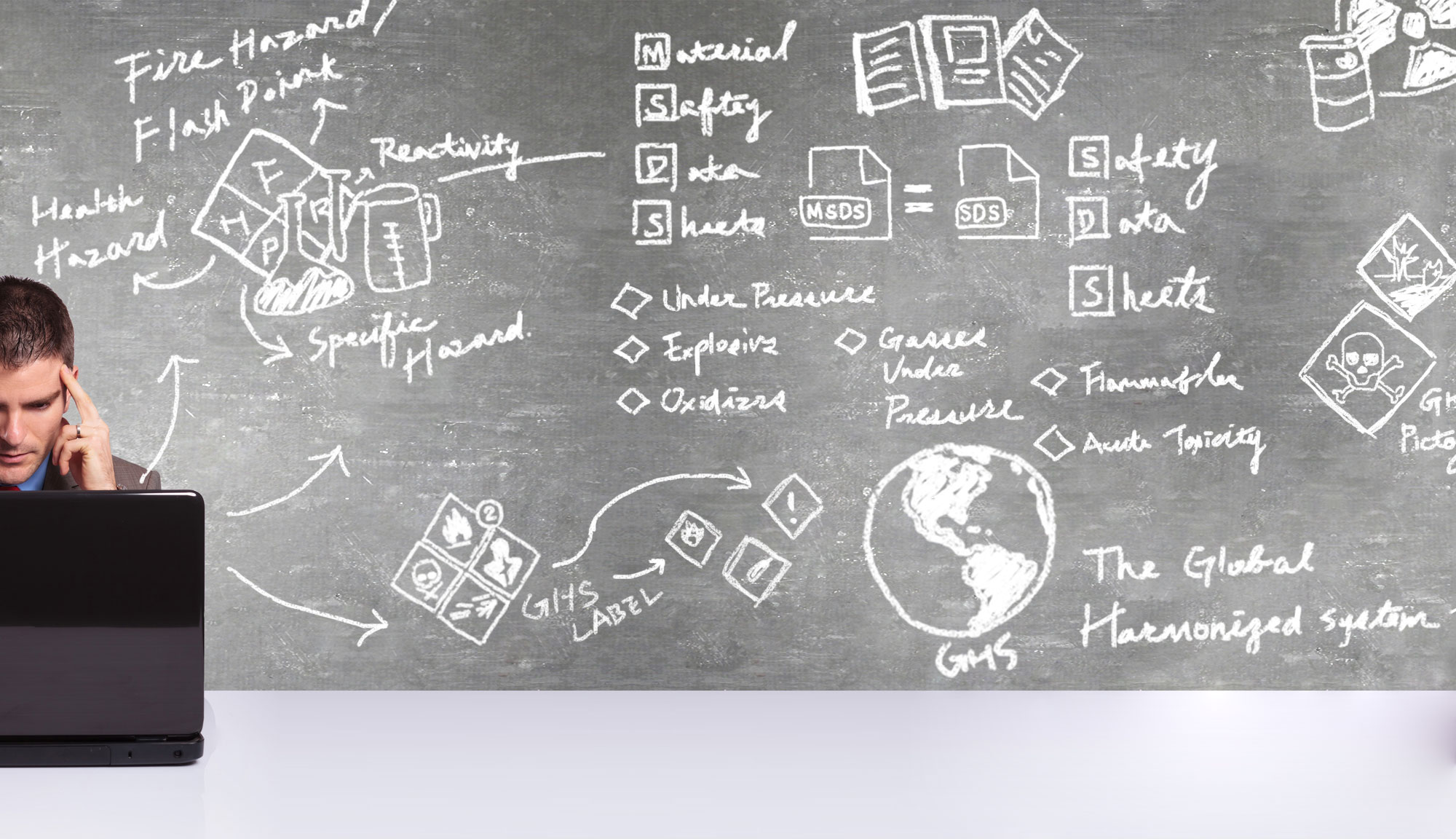
New OSHA Rules and Regulations
Aligning the Hazard Communication Standard with GHS is only one of the facets of OSHA’s safety campaign. Several standards are in development as OSHA strives to continuously improve safety and health regulations across America.
As per the national Department of Labor’s official Spring 2015 Agency Rule List, several pertinent rules are in different stages of development. Manage all your GHS information from one centralized location
Some rules that are relevant to Quantum and its clients’ interests are as follows:
The Process Safety Management standard is currently in the “prerule” stage. Changes to this standard affect regulations for the prevention of chemical accidents and will directly affect small business practices as well. Manufacturers and distributors need to be aware of changes to chemical safety standards, and can keep track of their safety practices using software like Quantum’s.
Regulations about combustible dust are also in the “prerule” stage. The last time that combustible dust definitions were updated was 2006, but OSHA does not currently have any formal standards about combustible dust regulations. As this affects HCS/GHS classification standards, the ruling may be important to determining specific safety guidelines for your company’s specific products.
Coal miners affected by industry-specific diseases are eligible for protection under the Black Lung Benefits Act. Two motions (one about medical benefits and the other about disclosure of information and payment of those benefits) are currently in the “proposed rule” stage. These rules, once completed, will have implications for workers and companies who need to compensate those workers for their afflictions. Though these deal specifically with coal miners and regulations that protect them, they may also have implications for workers in all dangerous industries.
Illness and injury reporting is one major component of the safety services that Quantum’s software can provide. A proposed ruling about Clarification of Employer’s Continuing Obligation to Make and Maintain Accurate Records of Each Recordable Injury and Illness will affect the legal standing of your company’s records.
One ruling in its final stages of completion is the proposal to update OSHA Standards Based on National Consensus Standards Eye and Face Protection. Under section 6(a) of the OSH Act, during the first two years of the Act, the Agency was directed to adopt national consensus standards as Occupational Safety and Health Administration (OSHA) standards. Some of these standards were adopted as regulatory text, while others were incorporated by reference. In the more than 40 years since these standards were adopted by OSHA, the organizations responsible for these consensus standards have issued updated versions of these standards. However, in most cases, OSHA has not revised its regulations to reflect later editions of the consensus standards. This proposed ruling would update those regulations for certain industries, among them shipyard and construction work.
HazCom Ranks as #2 Most Cited OSHA Standard
Out of OSHA’s top ten most cited standards, the Hazard Communication Standard (HCS) ranks as the number 2 most frequently cited standard. How does this affect you and your business?
According to OSHA, the smallest companies with only 1-19 employees, contributed to $70 million in penalties. In contrast, the largest companies with more than 250 employees were fined a total of $16.2 million.
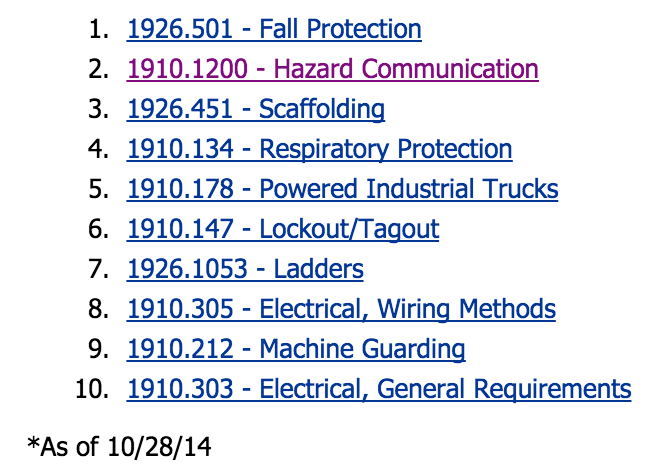
The numbers indicate an inversely proportional relationship between the company size and the number of safety violations. This inverse relationship may be attributed to smaller companies having limited resources to comply with safety and health regulations.
The Hazard Communication Standard is now aligned with the Globally Harmonized System of Classification and Labeling of Chemicals (GHS). Aligning HCS with GHS has allowed improvements in the quality and consistency of hazard information in the workplace, making it safer for workers by providing easily understandable information on the safe use of hazardous chemicals.
June 1st 2015 marked the GHS deadline for manufacturers to convert their existing MSDS (Material Safety Data Sheet) to the new GHS compliant SDS (Safety Data Sheet). With HCS being the second most frequently cited standard even before GHS took effect, understanding HCS in alignment with GHS is critical for employers to remain in compliance.
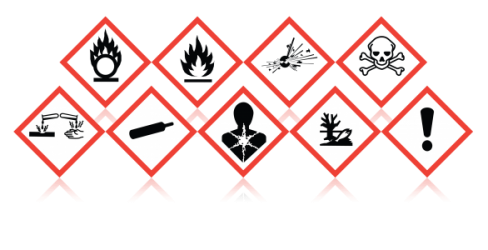
To avoid regulatory compliance fines, smaller companies should take extra steps to understand the many changes to HCS. A solution for smaller companies is to partner with a reputable safety solution provider. OSHA has stated that, “workplaces that establish safety and health management systems can reduce their injury and illness cost by 20-40%.” By investing in safety, not only will companies save in preventable costs, they show their commitment to their workers by protecting and ensuring their safe return home to their families.
For more information on HCS in alignment with GHS, check out our resource center by clicking the button at the top of the page above “Contact Us”.
HazCom 1983 “Right to Know” vs. HazCom 2012 “Right to Understand”
Since it’s conception 22 years ago, the Hazard Communication standard has dramatically increased the availability of chemical information in workplaces. Additionally, the legislation has dramatically improved the safety and health of workers who handle hazardous chemicals. Building off the success of HazCom 1983, HazCom 2012 works to move nations around the world in alignment with a Globally Harmonized Standard (GHS). The adoption of GHS is expected to prevent even more injuries and deaths, while simultaneously improving working conditions for chemical manufacturers.
OSHA has stated in their Hazard Communication Standard Final Rule that HazCom 1983 provides workers with the “right to know” about chemical hazards, whereas HazCom 2012 provides workers with the “right to understand”. At first glance “the right to know” and “the right to understand” may seem similar. However, according to OSHA, “several studies show that employees do not understand approximately one-third of the safety and health information listed on (MSDSs) prepared in accordance with the current standard.” This illustrated the fact that simply having MSDS’s available for a worker is not enough to communicate the potential hazards of dangerous chemicals.
Under HazCom 1983, to verify if companies were making hazardous information “known”, OSHA inspectors checked if MSDS’s were on file and whether corporations had records of workers trained. At this time, OSHA has not come forward and stated how they would verify if hazardous information is “understood”, but some have suggested that OSHA inspectors could possibly quiz workers on their understanding of pictograms and labels.
Training employees on GHS regulations is a critical step in the GHS adoption timeline. December 1, 2013 was the deadline for employers to train their employees on the new GHS standards. By carefully documenting the training workers have gone through, employers can remain in compliance as well as ensuring that their employees understand all the information relating to HazCom 2012.